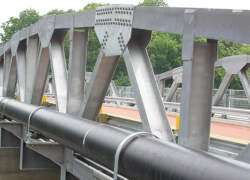
Superstructure
Reduce road closures and congested traffic due to road work with the corrosion protection and maintenance-free longevity hot-dip galvanizing provides.
The Federal Highway Administration (FHWA) and American Association of State Highway Transportation Officials (AASHTO) continue to focus on sustainability and more specifically building 100-year bridges, there are a number of bridge elements where hot-dip galvanizing (HDG) can play a vital role. The superstructure (everything above ground level) presents several opportunities to utilize HDG whether in visually showcased elements such as arches and trusses or more hidden ones - girders, cables, decking, or other ancillary items.
When designing with hot-dip galvanized steel, it is important to understand there are size constraints as the steel parts must fit into the galvanizing bath. In North America, the average kettle size is 40 feet, but there are many 50-65 foot kettles scattered around the country. However, there are a few ways to increase the size of the bridge members that can benefit from galvanizing including modular design, progressive dipping, and using a metallizing/galvanizing combination.
The easiest way to galvanize longer bridge spans is to design in modules or sub-units that fit the galvanizing kettle in one pass. This eliminates any challenges introduced by progressive dipping and provides savings in manufacturing and assembly as well as transportation. The sub-units can be connected after galvanizing by field-welding or bolting. A great example of modular design is in the first fully galvanized bridge in the United States, the Stearns Bayou Bridge installed in 1966. Another innovative design using modular galvanized units are press-brake tub girders, which also allow for a precast deck to be placed before shipping – providing great accelerated bridge construction (ABC) benefits.
If designing in modules is not possible, there are a couple of ways to utilize hot-dip galvanizing on longer bridge spans. The first is to use progressive dipping. Progressive dipping is the process of coating half of the steel beam, then flipping the steel to dip the remainder. To progressively dip, half the length or height of the article must fit into the kettle, so in essence progressive dipping can double the length of article that can be hot-dip galvanized.
If the span is still too large to be fully coated using progressive dipping, the final alternative would be to use a combination of HDG and metallizing. There are many ways to accomplish this including dipping the two ends of the piece and metallizing the middle, or metallizing all steel pieces that are too large for the kettle and then galvanizing the other pieces. Metallizing and galvanizing have very similar appearances and comparable durability, and because both are zinc coatings, there is no concern about dissimilar metals in contact.
Superstructure Components
Arches |
Bailey Bridge Structures |
Base Plates |
Beams |
Bearing Plates |
Bolts |
Cable Connectors |
Cables |
Columns |
Cross-Bracing |
Diaphragms |
Expansion Joints |
Folded Plate |
Girders |
Pedestrian Overpass Bridge |
Pot Bearings |
Press Brake Tub Girders |
Rolled Beams |
Shear Studs |
Splice Plates |
Spiral Shear Connectors |
Stringers |
Temporary Bridges |
Truss |